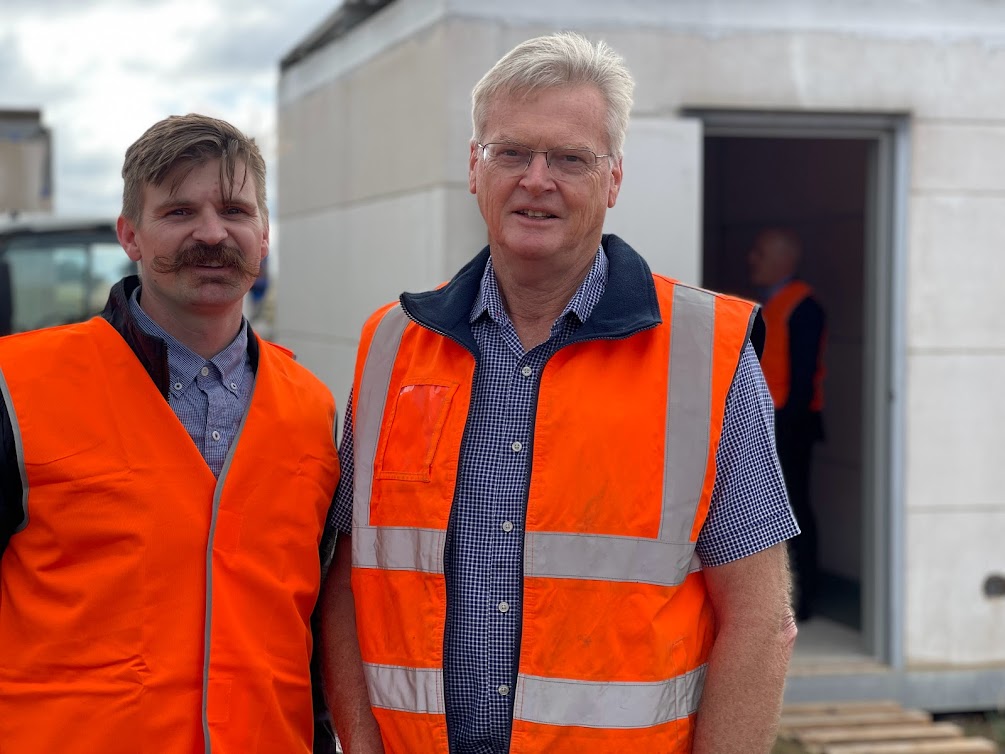
Tony Balding (right) pictured with son Mat, is working on an innovative approach to social housing. Photo: Adam Drummond.
It was while working to develop a transportable fire shelter that the team from Wagga’s The Building Supply Company saw the potential for something more.
The socially-minded company has expanded on the lessons learned from their fireproof modules to developing a robust, low-maintenance option for social housing.
“We determined that we could look at fireproof housing and expanding sizes and coming up with some innovative engineering concepts,” managing director Tony Balding explains.
Tony and the team began kicking around ideas for fireproof structures following the devastating Canberra bushfires in 2003.
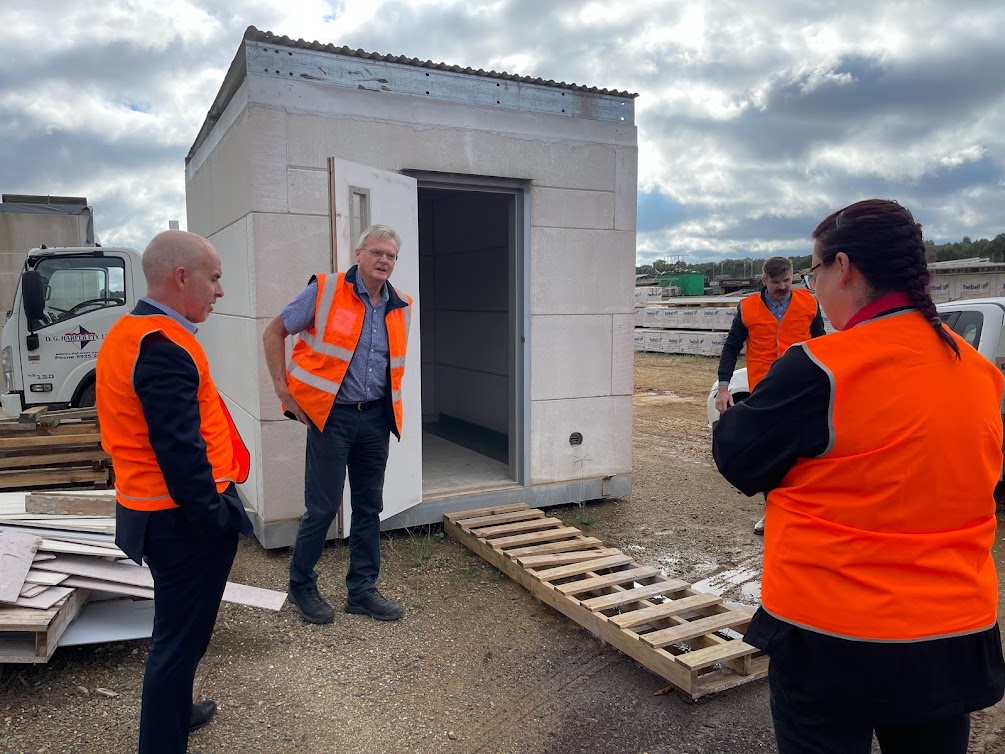
Tony’s Hebel fire shelters are currently going through testing with the CSIRO. Photo: Adam Drummond.
In 2012, they connected with the CSIRO and CSR Building Products and began developing the transportable shelter as an alternative to in-ground bunkers.
“They can be dropped in the back of houses or bush lanes in whatever way that can give people some refuge,” he says.
As they experimented with designs, Tony says they realised that the same materials could be used to produce a unique style of pre-fabricated housing.
“We have a social conscience ourselves and we’re thinking that if we have a product that can show what can be done on a reasonably quick return on the building process, we may be able to ease up some of these rental problems,” he says.
Hebel aerated concrete makes the elements easily transportable and the final structure highly durable.
“It’s a third of the weight of concrete and we don’t have any wall cavities, we don’t have any gyprock, all doorframes are solid steel grouted into walls. All the doors are solid and the windows are double glazed,” he says.
“There is a significant difference just in the quality of living in those houses.”
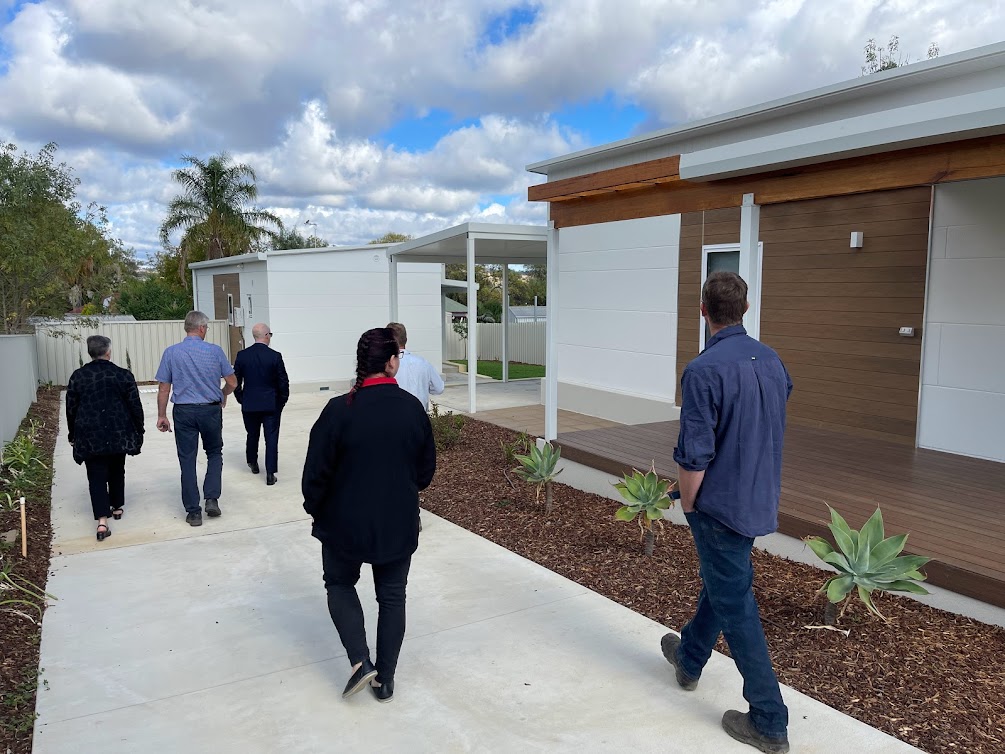
The team at The Building Supply Company has completed three social housing projects. Photo: Adam Drummond.
The NSW state government has taken an interest in the idea and three properties have now been completed for the social housing market.
“The long term value to the government would be minimal maintenance and a much better quality housing product for the tenants,” he says.
In January last year, the company moved into a new facility in the Bomen Special Activation Precinct where Tony says around 60 per cent of the building can be done.
“You’re not bringing a lot of trades on-site and working across each other all the time and sequencing the work becomes a lot easier to do,” he says.
Keeping most of the construction in the factory also assists in training and reduces waste.
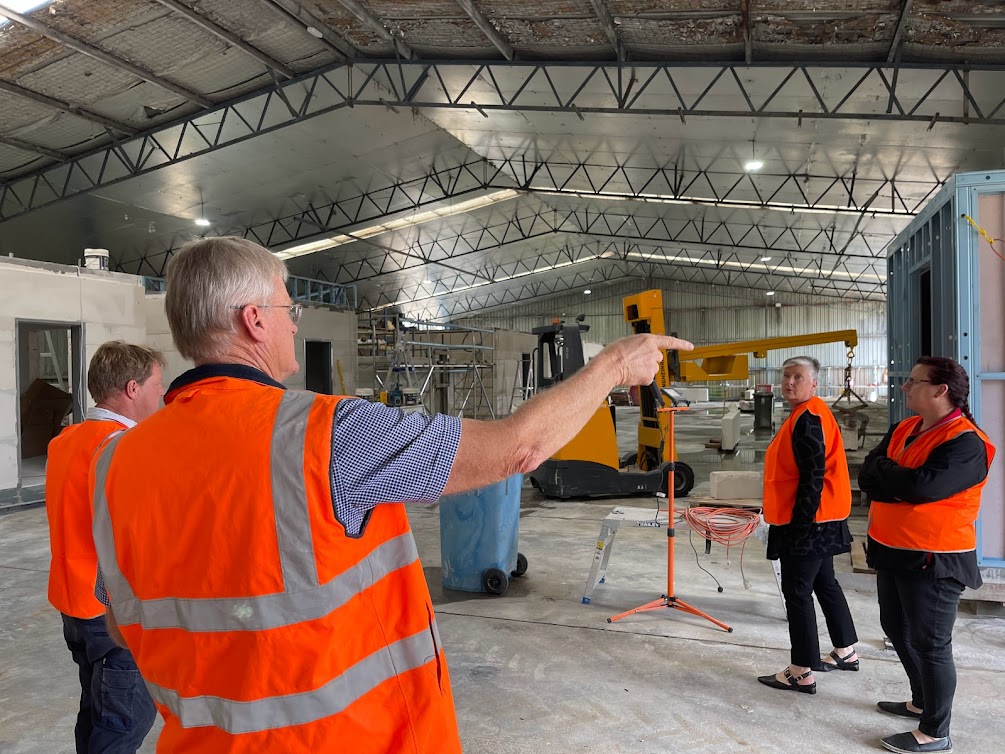
Sixty per cent of the work is done in a purpose-built facility at Bomen. Photo: Adam Drummond.
Wagga’s supply of social housing has been under considerable pressure in recent years.
Local MP Dr Joe McGurr says he’s raised the issue with Premier Dominic Perrottet and planning minister Anthony Roberts.
“They’ve actually got 60 new housing places coming online in the next 18 months and the Tolland renewal process is continuing,” he says, indicating the Argyle Community Housing project underway in Wagga’s south.
The initiative focuses on delivering a mix of affordable and social housing, emphasising community and lifestyle.
“It won’t only deliver better social housing, but it will increase housing supply as well and it will change the configuration, so there is a very big opportunity in that,” Dr McGirr says.
Tony Balding adds that the Tolland project is “a great example” of what the state government is trying to do but there is plenty more opportunity to explore.
“We also think there’s room to do a street-by-street upgrade, not just in one suburb, but where we can identify streets that need to be rejuvenated,” he says.
In the meantime, Tony and the team continue developing a range of designs that can be rolled out quickly to meet government or private demand.
“We’d like to think that we can give a long term product to social housing with minimum maintenance,” he says.
As for the fireproof shelters, they hope to complete testing with the CSIRO after the next fire season.
“It’s a work in progress,” he says.