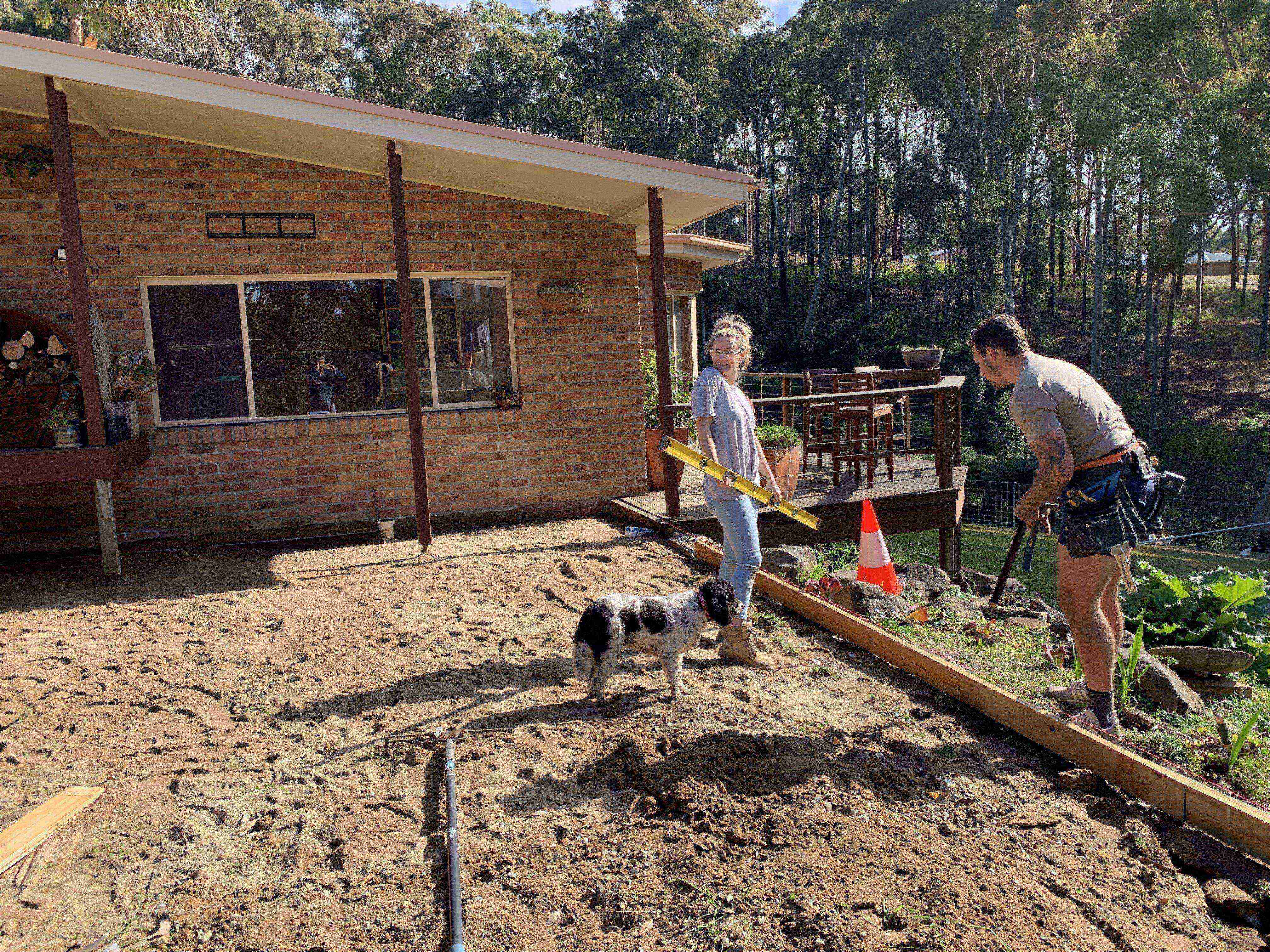
Construction work around the region is being severely hampered by a lack of materials. Photo: Kim Treasure.
New home buyers are facing delays and price increases as builders struggle to cope with mounting materials and labour shortages in the midst of a housing and infrastructure boom.
They are being warned to expect budget blowouts and extended completion dates while builders see their profit margins wiped out by rising costs.
Industry sources say it is a perfect storm whipped up by the impacts of the pandemic on global supply chains and the white-hot demand for housing driven by record-low interest rates.
In bushfire-affected areas the situation has been exacerbated by the push to rebuild or restore more than 1000 homes lost or damaged on the Far South Coast.
On the ground, it means a scramble for materials as builders try to secure supplies, with reports of orders being gazumped by those willing to pay more.
Some builders are revising or even rescinding contracts to stay ahead of the wave of price increases and there are fears that some might not survive.
One of Queensland’s largest residential builders, Privium Group, faces a $28 million collapse amid warnings of a profitless boom.
Master Builders ACT CEO Michael Hopkins said the construction industry was facing a serious issue with a combination of soaring prices, delivery delays and labour shortages.
Mr Hopkins said members had reported dramatic price increases from suppliers this year, which in some cases have been more than 30 per cent.
“Initially, we heard about shortages of timber, then shortages and price increases for steel,” he said.
“But we’re now hearing that most building products are experiencing price increases and shortages including glass, windows, insulation, as well as timber and steel.”
That means new builds and renovations will take longer and cost more, and he urged people to discuss the situation with their builders.
“What we’re seeing is that these cost increases are pretty well consuming the profit margin and in some cases, making projects unviable,” Mr Hopkins said.
Mr Hopkins said the lockdown had already devastated small businesses, and now they were being hit by this.
Business closures may not happen immediately but by the second half of next year, the pressures could drive some to the wall and they might not just be the smaller operators.
“We’re finding this is impacting the very largest to the smallest contractors,” Mr Hopkins said.
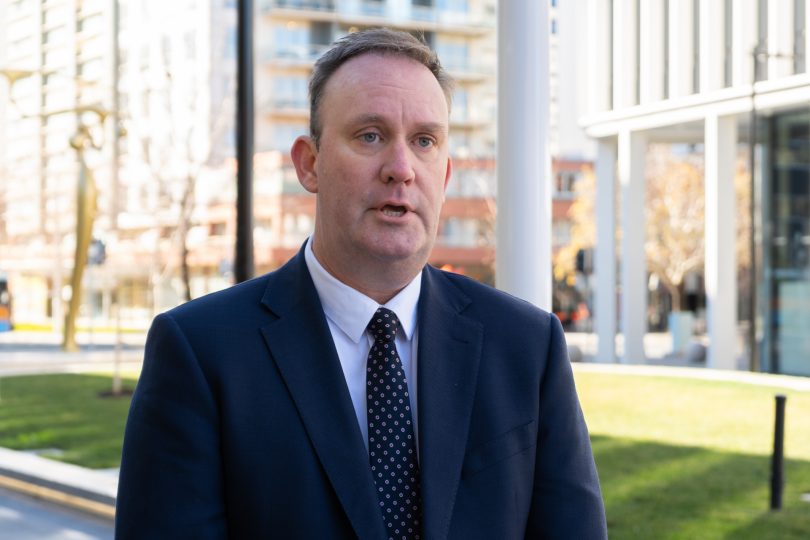
Master Builders ACT CEO Michael Hopkins: “What we’re seeing is that these cost increases are pretty well consuming the profit margin and, in some cases, making projects unviable.” Photo: File.
He said industry was working closely with the federal government to identify and clear supply chain blockages.
Civium Property Group’s director of project sales Matt Nicholls said he had never seen a situation like this before.
He said builders were faced with price increases such as steel being up 10 per cent, concrete reinforcement 20 per cent and timber 25 to 30 per cent and unless they were locked into contracts, they had to be passed on to the home buyer. Some were absorbing what they could, but others would be taking a loss, Mr Nicholls said.
He said this was being exacerbated by delays of up to 12 weeks – “and that’s a lot of money when you’re holding the land” – translating to completions on average overdue by three months or longer.
“I know a builder who paid upfront for steel and lumber three or four months ago and they’re still waiting,” he said.
“We’re dealing with developers who have delayed their release until February next year to make sure they can get enough stuff and get going.”
Mark Kingston, of Cameron’s Hardware Moruya, has worked in the trade for 50 years and says he’s never seen anything like the current conditions.
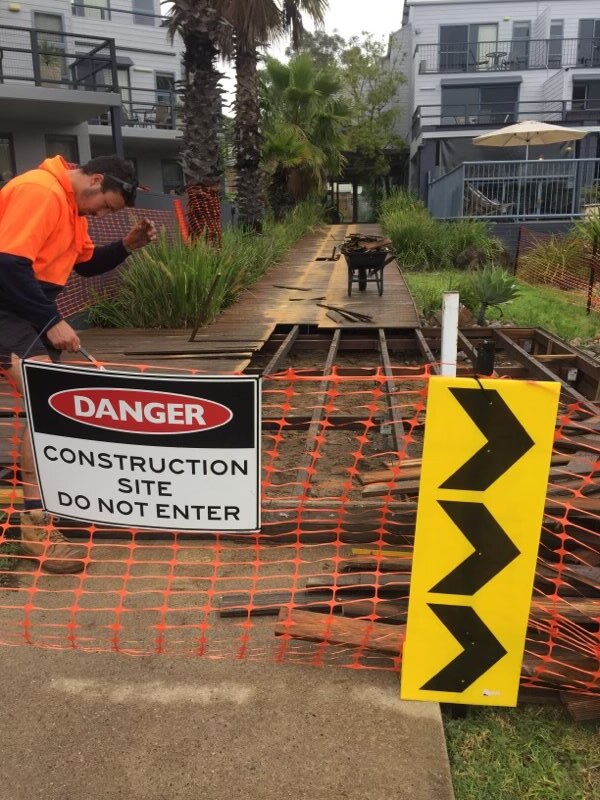
Grant Crapp, of GDC Carpentry and Electrical, at work in Batemans Bay. Photo: Lucy Cartwright.
“It’s very frustrating,” he said. “My racks are half empty and a lot of material you are just unable to get. Some we ordered 12 months ago and it’s just coming in dribs and drabs. It’s pre-sold before you can even blink and it’s getting a lot worse.
“From steel mesh to concrete … we can’t even get insulation now.
“We knew this was coming 18 months ago and now it’s catching up with us and it’s going to get worse.
“The builders are understanding. They are ordering months beforehand and just sweating on it coming in on time.”
Batemans Bay contractor Grant Crapp, of GDC Carpentry and Electrical, said the shortages and price hikes were making it difficult to meet client expectations in the run-up to Christmas.
“So far we’ve managed to get all our work done on time and on budget but the pressure of sourcing the materials we need is just adding to the stress at a really busy time of year,” he said.
“We’ve come through the bushfires and then COVID-19 and it should be full steam ahead but these shortages could put the brakes on well into next year.”
Original Article published by Ian Bushnell on Riotact.