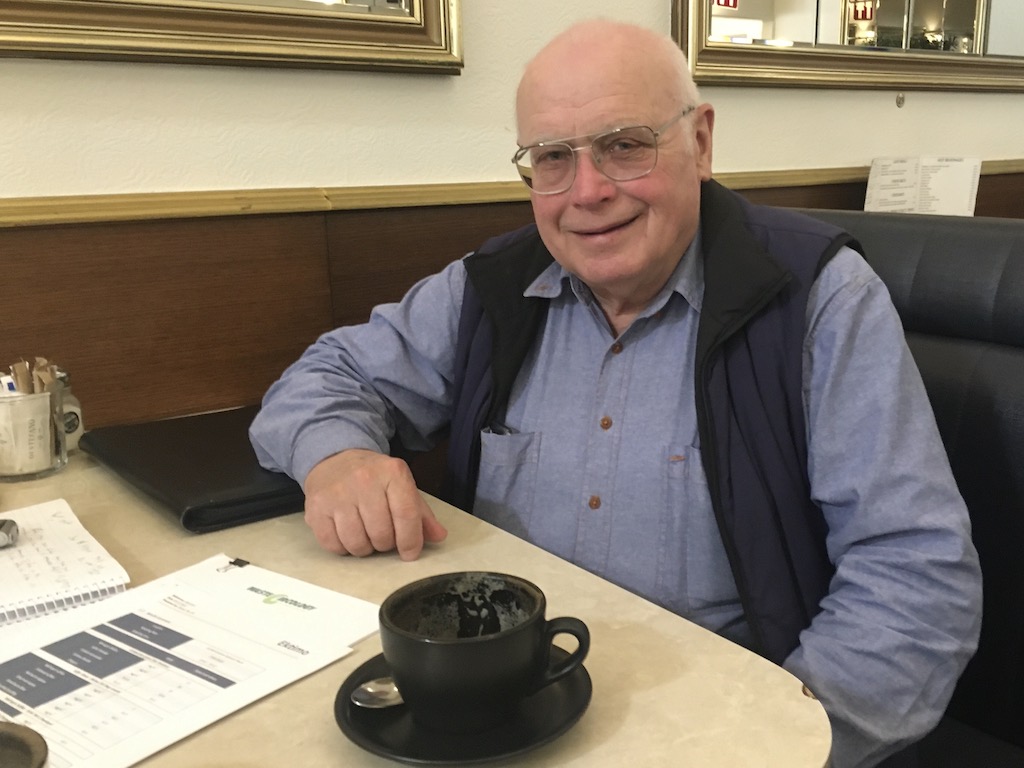
Ken Halliday has guided multiple business ventures from Goulburn, and now finds himself helping one with an eye on waste streams around the country and abroad. Photo: John Thistleton.
When Ken Halliday first came to Goulburn in 1989 with the Soil Conservation Service, the local landfill on the city’s eastern edge was down a slight valley. Today it’s a small mountain of buried waste.
He draws on the landfill example to underline the intractable problem of polluting waste management that afflicts the city, the state, and indeed the world. The NSW Government’s solution for much of Sydney’s waste leaves a lot to be desired if you live in the Goulburn district – trainloads of waste filling an open-cut mine and the looming prospect of a $600 million incinerator to burn the stuff.
Ken Halliday belongs to a small start-up enterprise working on a cleaner alternative. The group has invented a reactor that converts organic, and even synthetic, waste (e.g. tyres) through carbonisation. Interestingly, its prototype reactor is not stuck out in the bush somewhere – it’s in South Strathfield, Sydney. That’s how low the emissions are from the semi-commercial processing plant.
So how did Ken find himself helping write the business plan for a team of civil and mechanical engineers and consultants around the country and Germany working on a solution for waste?
Through the 1990s, he watched Goulburn undergo a significant shift, with the highway bypass arriving and many government offices, and big private entities such as Oral B, leaving.
While the city was changing, so too was Ken. After working with Soil Con around NSW, he left and settled permanently in Goulburn in 2000 with his wife Ann and three children. He applied his accounting and bookkeeping skills to manage businesses with diverse pursuits, including a Goulburn medical centre and another that provided turkey farm litter that was reused as fertiliser.
One of his earlier projects was on the tail end of demolition and earthworks associated with Westfield Shopping Centre in Burwood.
“An incredible experience, that – an entire city block in Burwood was demolished, rebuilt and opened within 12 months,” Ken said.
It was an excellent learning experience on crushing and reusing concrete for the base of the new building. Another interesting project was the remediation of the final section of the old Chullora railway yards on the Cooks River. The removal of more than 4000 cubic metres of hydrocarbon-contaminated soil for thermal disposal was a highlight.
In Goulburn he caught up with a friend, accountant Peter Bugden, and helped small businesses come to grips with the introduction of the Goods and Services Tax.
His clients were varied, putting him in touch with Gary Allan, who has more than 40 years of military, government and commercial experience in general and senior management, and Jerry Lissing, who came from a hospitality-oriented family who previously owned hotel chains around Australia.
From these connections, he met civil engineer Joseph Taouk and the remaining team on Waste Circology. Ken is revelling in his business and administration role.
“With the scope of experience I’ve had in agriculture, plant work and research, it’s a good mix that comes into play and we have been able to provide that mix to Waste Circology,” he said.
Joseph’s background in construction led to his interest in waste management, research and developing an organic carbonisation system. This low-emissions process transforms organic waste into a rich char-carbon compound.
Joseph’s family has invested $3m in establishing the trial plant and ongoing research. To scale up into full commercialisation will require between $40m and $50m of investment funding.
Waste Circology was invited last October to present its technology at Bio360, a global gathering of bioenergy companies, in France.
“The people involved with producing biochar by pyrolysis could not believe that there was this process being developed that could reduce it a lot faster with minimal emissions – all the emissions are below Environmental Protection Authority standards,” Ken said.
“We presented a scientific review on how biochar can help remediate sandy soils and degraded lands to the ambassadors for Kuwait and Qatar in Canberra. Both countries have massive problems with waste, and are seeking ways to reuse it to benefit the landscapes.
“The interest in this has been phenomenal. BlueScope Steel wants 100,000 tonnes of biochar produced by this process per year to replace coking coal, which means they don’t have to dig coal out of the ground, they can use reduced forest waste to biochar. That’s a big win.”
Timber exporter Pentarch Forestry is clamouring for a solution to its waste in Grafton, while investors in South Australia are interested in processing destroyed timber from bushfires on Kangaroo Island, rather than leaving it on the ground. In India, a car tyre processor would be happy to use syn (synthetic) char to replace coking coal, and wants enough for nine steel mills.
Meanwhile, managing waste today by burying and burning is unwelcome in many regions, including Goulburn. But science is offering alternatives that return core ingredients to the earth for soil enrichment, among many other beneficial processes.