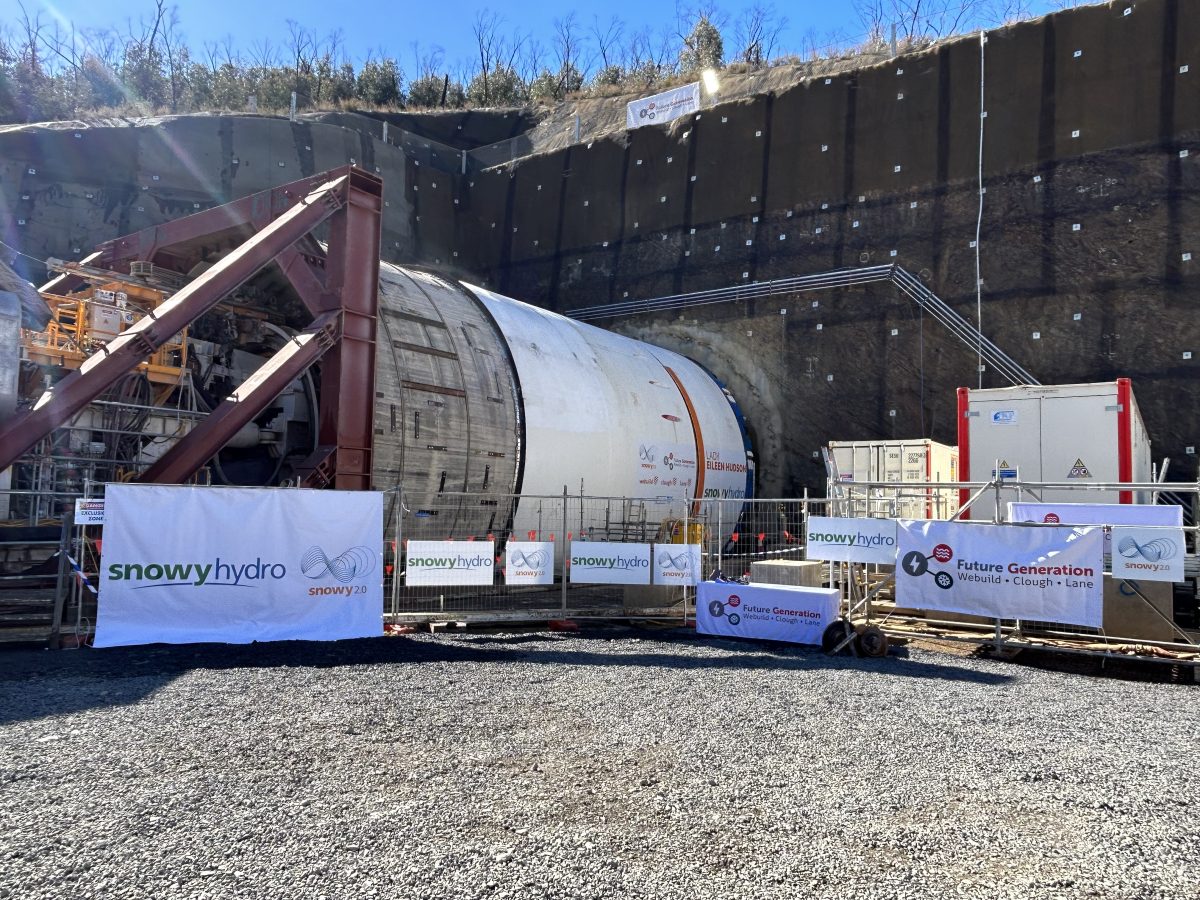
Tunnel boring machine, Lady Eileen Hudson, has been relocated for the next stage of the Snowy 2.0 Project. Photo: Snowy Hydro.
July marked an exciting milestone for Snowy Hydro, the Snowy 2.0 project and for one of its three tunnel boring machines.
Tunnel boring machine (TBM) Lady Eileen Hudson was the first machine to start tunnelling on the pumped-hydro mega project, the first to complete a tunnel and is now underway on her second tunnel excavation.
Snowy 2.0 senior project manager, Rodd Brinkman, is onsite at the Talbingo adit, where teams have been preparing to relaunch TBM Lady Eileen into the mountain.
The TBM will excavate the 6 km tailrace tunnel to connect Talbingo Reservoir to the underground power station complex.
Water used to generate 2000 megawatts of power from Snowy 2.0 will flow out of the tailrace tunnel. Water also enters this tunnel when the power station is pumping.
After completing the 2.8 km main access tunnel (MAT) in 2022, it has been a big task to disassemble and safely extract TBM Lady Eileen and reassemble her with new components before commissioning. The conveyor stacker, grout batch plant, and chiller plant were also relocated from the MAT portal to the Talbingo adit.
Before a TBM begins her journey underground, it is traditional for the machine and crew to be blessed for a safe journey under the watch of St Barbara, the patron saint of tunnelling and underground work.
The tradition of blessing is acknowledged at tunnelling sites all over the world.
Local parish priest Father Mark Croker blessed the TBM at an onsite ceremony with many Snowy 2.0 workers in attendance.
The machine was then switched on and began cutting the rock face. This is the fourth TBM launch for Snowy 2.0 and a major achievement for the Snowy Scheme expansion project.
TBM Construction Manager Derek Whelan manages all Snowy 2.0 tunnelling activities, as well as the TBM construction personnel. He was on-hand to run through Lady Eileen’s impressive components, including a new 378-tonne cutterhead.
The cutterhead is made up of 70 cutting discs, each weighing 290 kilos, that will excavate the varying geology of the 11-metre diameter tunnel. At 137 metres in length and weighing 2300 tonnes, the TBM is a moving factory with many parts working together in a complex operation.
More than 27,000 concrete segments manufactured at the Polo Flat, Cooma, precast facility will be used to line the tailrace tunnel with the segment erector, segment feeder, segment cranes, and sophisticated grouting system all onboard the TBM.
The TBM is also equipped with a guidance system that provides data to the machine’s pilot, to the nearest millimetre. This information is mirrored above ground and monitored by Snowy 2.0’s construction and engineering teams.
Another positive for the Snowy 2.0 project is the successful ground stabilisation works and construction of a slurry treatment plant at Tantangara carried out by Snowy 2.0 teams prior to TBM Florence being able to restart the excavation of the headrace tunnel.
Final commissioning tests are underway for the onsite slurry plant, which means the dual-mode machine can switch from open excavation to a closed, pressurised mode. This excavation method will enable stable excavation and efficient progress through softer ground conditions when required.
A significant testing regime has confirmed grouting and stabilisation of the loose material around TBM Florence has been effective.
Additional stabilisation continues from the surface to solidify loose material above the machine and directly in front of the TBM cutterhead and the rock mass the machine is just short of.
Snowy is carrying out rotations of the cutterhead and minor advances of TBM Florence to ensure the machine is correctly positioned for final commissioning and to confirm the ground support activities are working.
Snowy is working with NSW departments on environmental approvals for remediation of the surface depression above TBM Florence and to provide assurance that this will not reoccur.
The plan is likely to go on public display in the coming weeks.
The slurry treatment plant will process and separate materials used when the TBM is in closed excavation mode, including bentonite (an absorbent, swelling clay), which is placed into a tank and reused.